In industries where safety, reliability, and operational efficiency are paramount, Non-Destructive Testing (NDT) plays a critical role in ensuring asset integrity. Among the most advanced and effective NDT methods available today is Phased Array Ultrasonic Testing (PAUT)—a superior alternative to conventional ultrasonic and radiographic testing.
At CATSI, we integrate PAUT into our advanced NDE solutions, delivering real-time, high-resolution imaging, enhanced flaw detection, and improved inspection efficiency. Our recent success in identifying critical defects—missed by traditional inspection methods—demonstrates the power of PAUT in preventing costly failures and ensuring structural integrity across multiple industries.
What is Phased Array Ultrasonic Testing (PAUT)?
PAUT is an advanced ultrasonic examination technique that utilizes multiple elements in a single probe to steer and focus ultrasonic beams dynamically. Unlike conventional ultrasonic testing (UT), which relies on a fixed-angle beam, PAUT electronically sweeps the inspection area, providing a comprehensive and detailed view of internal structures.
This capability allows for multi-angle scanning, real-time imaging, and greater accuracy in detecting and characterizing flaws, including:
- Cracks
- Lack of fusion or penetration
- Porosity and inclusions
- Wall thinning and corrosion
By eliminating gaps in coverage, PAUT significantly improves defect identification while reducing the need for multiple test setups, making it ideal for critical weld inspections, corrosion mapping, and structural integrity assessments.
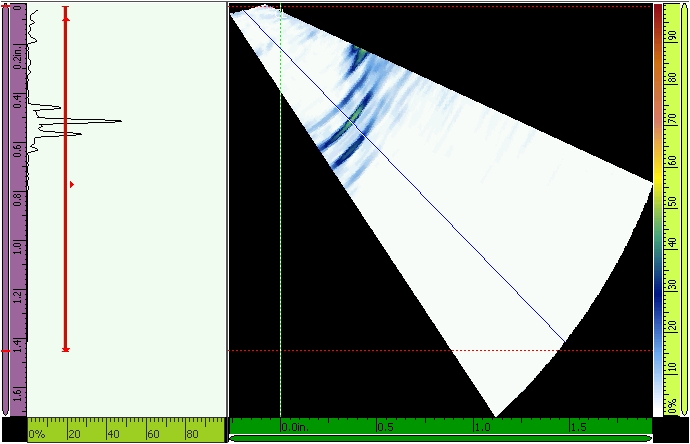
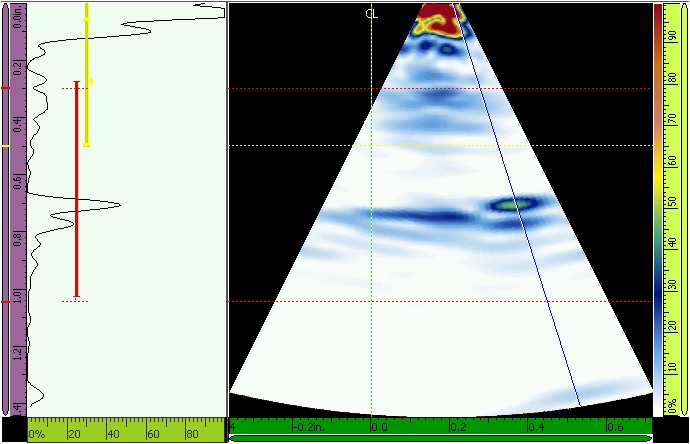
Key Advantages of PAUT Over Conventional Methods
1. Superior Flaw Detection & High-Resolution Imaging
PAUT provides real-time, high-resolution images of internal structures, enabling precise defect characterization. Unlike manual UT, which relies on single-angle amplitude signals, PAUT generates cross-sectional and 3D views, making it easier to interpret results and identify hidden defects.
2. Faster Inspection, Reduced Downtime
Industries relying on continuous operations cannot afford extensive downtime for inspections. Compared to radiographic testing (x-ray), which requires film processing and radiation safety protocols, PAUT delivers:
- Instant results with on-site evaluation
- Minimal operational disruption—inspections can be performed without system shutdown
- Rapid data collection with multi-element transducers
3. Cost & Efficiency Benefits
PAUT improves efficiency by:
- Minimizing setup time
- Reducing probe changes
- Lowering overall inspection costs by shortening time spent on in-field inspections
For industries such as oil & gas, power generation, and manufacturing, PAUT provides a cost-effective alternative while maintaining compliance with stringent industry standards.
4. Complex Geometry Inspection
Unlike traditional UT methods that struggle with irregular or difficult-to-reach areas, PAUT excels in inspecting complex geometries, including:
- Curved surfaces (pipes, pressure vessels, turbine blades)
- Thick or multi-layered welds
- Intricate castings and forgings
This makes PAUT particularly beneficial for pipeline inspections, aerospace components, and power generation structures.
5. Safety Advantages: A Non-Radiation Alternative to X-Ray
Unlike radiographic testing (RT), which uses ionizing radiation, PAUT is completely safe for both inspectors and surrounding personnel. This allows inspections to be conducted without restricted access zones, special safety procedures, or environmental hazards, making it the preferred method in confined spaces and densely populated facilities.
6. Compliance with Industry Standards
PAUT is a code-approved and widely accepted method for weld and pipeline inspections, adhering to:
- ASME Section V (Boiler & Pressure Vessel Code)
- API 1104 (Pipeline Welding Code)
- AWS D1.1 (Structural Welding Code)
Many industries are now prioritizing PAUT over x-ray inspections, ensuring compliance while benefiting from faster and safer evaluations.
How CATSI Uses PAUT to Deliver Reliable Results
At CATSI, we incorporate PAUT into our advanced NDE services to ensure our clients receive precise, data-driven assessments for their most critical infrastructure.
In a recent inspection project, CATSI was brought in to examine welds that had previously been tested using traditional NDE methods. Despite the initial clearance from conventional testing, our PAUT scan revealed multiple defects, including a through-wall crack, that had been missed. Had these defects gone undetected, they could have led to:
- Major structural failures
- Unplanned shutdowns
- Significant safety risks
This case highlights why PAUT is superior to older NDE methods and how CATSI’s expertise in phased array ultrasonic technology helps clients mitigate risks, reduce maintenance costs, and prevent costly downtime.
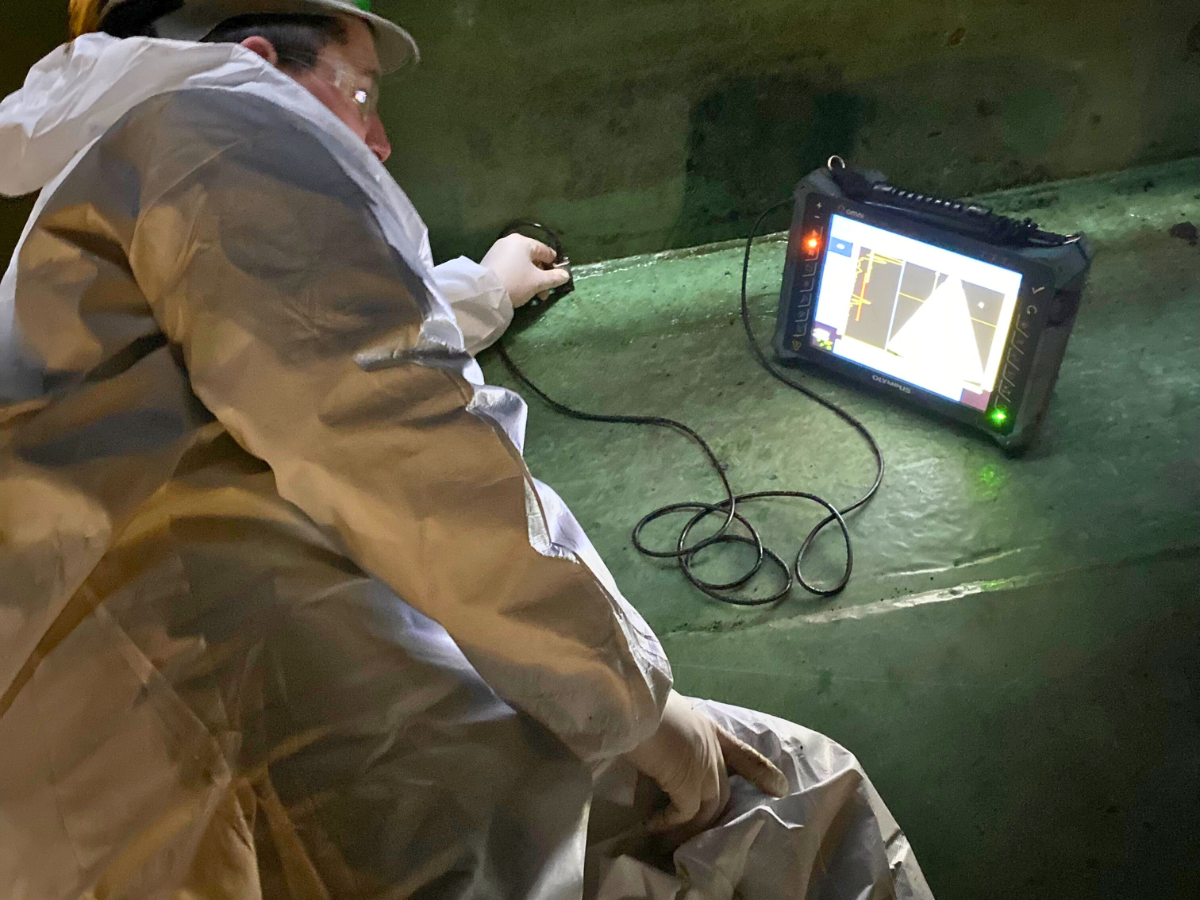
Industries Benefiting from PAUT
The versatility of PAUT makes it an essential tool across multiple industries:
- Oil & Gas – Ensuring pipeline integrity, detecting weld flaws, and assessing corrosion risks
- Power Generation – Inspecting boilers, turbines, and pressure vessels for defects and material fatigue
- Aerospace – Verifying aircraft component integrity to prevent fatigue failures
- Manufacturing & Construction – Conducting structural weld inspections to meet compliance standards
By implementing cutting-edge PAUT technology, industries can:
- Improve safety
- Maintain compliance
- Reduce maintenance costs
- Extend the lifespan of critical infrastructure
CATSI: Leading the Way in Advanced Inspection Solutions Tailored to Our Clients’ Needs
With decades of NDT experience, we deliver inspections grounded in safety, quality, and precision—using the latest technology and adhering to the highest industry standards.
Through the application of Phased Array Ultrasonic Testing (PAUT), CATSI continues to push the boundaries of what is possible in non-destructive testing, identifying flaws that traditional methods might miss. Our approach ensures that industries—from oil and gas to aerospace—are equipped with the insights they need to make informed decisions and enhance the longevity of their assets.
By embracing the most advanced testing techniques available, CATSI provides clients with not just results, but peace of mind in knowing their assets are safe, reliable, and built to last.
Citations & References
- American Society of Mechanical Engineers (ASME). (2024). ASME Boiler and Pressure Vessel Code, Section V: Nondestructive Examination. Retrieved from https://www.asme.org
- American Petroleum Institute (API). (2023). API 1104: Welding of Pipelines and Related Facilities. Retrieved from https://www.api.org
- American Welding Society (AWS). (2024). AWS D1.1: Structural Welding Code – Steel. Retrieved from https://www.aws.org
- International Society of Automation (ISA). (2023). Introduction to Phased Array Ultrasonic Testing. Retrieved from https://www.isa.org
- U.S. Department of Energy (DOE). (2024). Ultrasonic Testing and Phased Array Technology in the Energy Sector. Retrieved from https://www.energy.gov
- NDT Resource Center. (2023). Phased Array Ultrasonic Testing: Principles and Applications. Retrieved from https://www.ndt-ed.org
- The Welding Institute (TWI). (2023). The Benefits and Applications of Phased Array Ultrasonic Testing (PAUT). Retrieved from https://www.twi-global.com
- Non-Destructive Testing (NDT) of Materials. (2022). A Comprehensive Guide to Phased Array Ultrasonic Testing. Retrieved from https://www.ndt.net